By
Professor Okanga Boniface
London, England, 6 January, 2025
As the fourth industrial revolution becomes a reality to reflect more advancement in AI, robotics and machine learning technologies, the advancement of digital twin technology will also turn into the next big thing in the fourth industrial revolution era. Digital twin scans and translates physical objects or products into virtual representation. Whether the business is developing a new medical drug, device, equipment, or a building, digital twin scans the product to offer the desired virtual insights of the physical product (Cole, 2024). The end result is the twin representation of the product constituting of the digital virtual product and the actual physical product. If the business is developing a new baby formula, car, building or water treatment plant, Microsol Resources’ (2024) video below implies digital twin creates the virtual representation of the final product. This enables product developers map, compare and contrast virtual representation and physical reality to discern the critical components required for making the product more appealing to the unfolding market trends.
Despite hefty costs and unique skills required for using digital twin technology, its seamless integration in business operation still bolsters a firm’s overall competitiveness. As businesses strive to create and deliver the best, increasing competition across all sectors is driving most of the innovative firms to explore the best ways of creating and delivering the best products. Businesses are exploring and seeking to exhaust all options aimed at creating a product that disrupts and reshapes the existing industry settings to their advantages. In that process, the advancement in artificial intelligence, robotics and machine learning technologies has offered new technological insights for creating and delivering some of the best products. Artificial intelligence improves the speed of product research, design, development and delivery to the market. It improves the accuracy of product design analysis as well as its capabilities to accurately respond to the unfolding market trends.
As part of the important developments in artificial intelligence, robotics and machine learning technologies, digital twin has emerged as one of the disruptive technologies that businesses are adopting to bolster their innovation superiority (Cole, 2024). Digital twin is the technological analysis that aids the representation of physical objects or products in virtual forms as well as the virtual representation of physical objects in digital forms. Digital twin enables innovation firms compare and contrast physical products with virtual ones. This improves the understanding of the required product components as well as the costs for developing a particular product. It improves the value of the ideation processes for the business to come up with an array of ideas on how the product can be improved. Digital twin enables innovation firms create and represent a prototype in virtual forms. This enhances accurate analysis and identification of the strong features of the product that define its competitiveness as well as its weaknesses requiring modifications and improvement.
During product design, a prototype could be fitted with sensors to enable the translation of physical product into virtual products. It is from such virtual representations that innovators are able to discern whether or not the product meets the specifications of what they intend to create and deliver. Digital twin reproduces the physical products into the virtual form to enable product developers discern the components required for making the product. This improves the accuracy and speed of new product development. It also lowers costs whilst also enabling innovators identify how to create new points of differences that improve the competitiveness of the product.
Digital twin puts the product in the form that enables innovators assess and re-assess the product. This improves the degree of creativity for the business to create and deliver products that surpass customer expectations. Through virtual representation of the physical product, Geospatial World’s (2024) video below suggests digital twin aids the proactive analysis of the behaviours of the product.
This reduces the costs of defects as well as the effectiveness of quality management. It also influences attainment of the desired product development outcomes. Digital twin often constitutes of four segments encompassing physical entity, digital model, data connection and analytics and simulation. Physical entity refers to the realworld product, business process, manufacturing processes, building, machine or service being modeled using digital twin.
Digital model is the physical object translated into a digital or virtual form. Data connection is the linkage created by sensors fitted on the physical product. Such sensors generate data to update the digital model about the physical product. It is from such updates that digital twin discerns the new required improvements. Analytics and simulations deal with critical analysis and simulation of the generated data to undertake predictive analysis that must be undertaken to improve product performance.
During product design, digital twin generates an array of design options to enable innovators select the best product design. It also eases the product testing and validation processes. Digital twin uses the product’s virtual representation to test and validate various areas of the product. Once the product is introduced in physical form, only minor changes and modifications are required to perfect the product. In the global automotive industry, it is Tesla that has emerged as the leading user of digital twin for testing and validating vehicle performance. Using digital twin, Tesla is able to create virtual representation of the designated electric car to be developed.
This enables evaluation of the efficiency of engine design and performance, battery performance and aerodynamics of the car prior to the development of the final physical cars. Using this approach, Tesla often does not need prototypes for testing and if it needs, the cost of prototyping can be quite lower. Because the product is presented in virtual form that does not cost anything to change, digital twin tends to aid iteration during product development process. This improves the capabilities of innovators to emerge with new insights that improve features, attributes and functionality of the product. Through digital twin and its data connection feature, the business is able to integrate predictive maintenance in new product development.
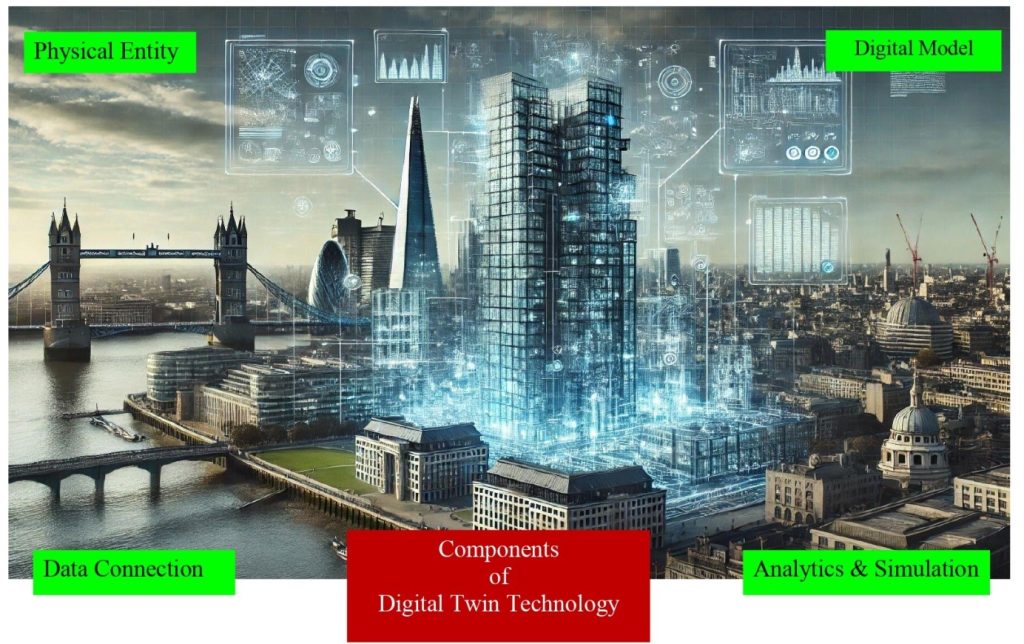
Even when the product is subsequently created, digital twin aids the efficacy of remote predictive analysis and maintenance. This improves product quality as well as the quality of after-sales services. It is from such insights that digital twin not only bolsters efficacy of new product development, but also a firm’s competitiveness.
Besides the global automobile industry, digital twin is also used in aerospace and defence engineering systems. During aircraft manufacturing, aircraft makers like Boeing have often used digital twin to create the virtual representation of the physical aircraft to be made. This has often helped in the assessment of the required components as well as the engineering technology and resources for making such aircrafts. During the development of 787 Dreamliner, digital twin was used to assess the stress exposure of the used materials if the aircraft is filled with the intended weight and it is in flight. This enhances iteration and improvements to create the 787 Dreamliner capable of holding the intended weight during flight.
In the aircraft manufacturing sector, digital twin improves lightweight analysis, design and evaluation of the required materials. It also enhances safety analysis in situations of extreme pressure as well as predictive and remote maintenance. Digital twin is not only essential for new product development, but also for process analysis, change and improvement. When Nestle wanted to change its Juuka food plant in Finland into a digital factory, digital twin became quite essential for discerning new systems that could be introduced.
Nestle’s Juuka food plant in Finland was an old food manufacturing plant charged with the manufacturing of high quality demi-glace, gravies and fonds for chefs and restaurants. Since its establishment, the Juuka food plant’s operation was molded along the old manufacturing systems.
Combined with its remote location in Finland, changing it from the old manual and analog-based manufacturing system to the required modern digital factory was not an easy task (Siemens, 2024). To ensure the success of such change and transformation, Nestle engaged and partnered with Siemens. Using digital twins, Siemens diagnosed and created virtual picture or representation of the required digital factory. Its virtual system put everything like workflow, manufacturing processes, peoples’ movement and networking as well as sourcing and relationship with suppliers and distributors.
Such analysis aided the analysis of the important areas that must be changed from the old Juuka food plant to create a modern digital factory. It also influenced Nestle’s decision to determine the required new digital machineries as well as manufacturing technologies that it must establish to influence its overall effective performance. Due to the support from digital twin, Nestle was able to ensure speedy diagnosis and implementation of the required digital change and transformation aimed at reconfiguring Juuka factory into a modern digital factory. Such initiatives depict how digital twin not only aids the development of new products, but also the invention and introduction of new operational processes. Due to its enormous business values, digital twin will become the next big thing in the fourth industrial revolution era.
Digital twin is essential for not only businesses like Nestle and Unilever that operate in the global food manufacturing segment, but also for the businesses operating in the private healthcare sector. In the United States and Germany, significant innovations have been undertaken to improve the seamless integration of digital twin usage in healthcare operations.
For healthcare diagnostics and imaging, digital twin technology has contributed enormously to improving the efficiency of digital imaging. It enables the accurate diagnosis and translation of physical humans into virtual humans presented on computer screens. This enhances capabilities of medical personnel to undertake thorough analysis to discern health problems affecting a particular patient (Scott, 2024).
While using digital twin technology, doctors are also able to simulate the efficacy of a particular medicine. Before the actual administration of medical drugs, doctors use digital twin to conduct simulation aimed at discerning medical drugs that would work. As depicted in Analytics Insight’s (2024) video below, this improves the efficiency and efficacy of medical treatment.
Digital twin improves not only capabilities to discern the right drugs, but also accuracy of medical diagnosis. It improves capabilities of medical personnel to accurately and quickly evaluate patients and come up with the right medications. When discerning the medication to be prescribed, digital twin helps doctors assess the probable allergies and side-effects of the drugs to be administered. After comparing several medications, it influences the selection and prescription of the best medications. This improves the quality of healthcare services.
Yet it is not only for medical diagnostic that digital twin tends to be of great value, but also in situations where healthcare operator aims to diagnose and improve the efficiency of the existing healthcare management processes. In such processes, digital twin scans and puts the physical healthcare processes into virtual forms. This enables medical facility undertake an holistic assessment of its critical processes to discern the areas requiring improvement to bolster the quality of the offered healthcare services.
For a business to integrate digital twin in its product development or process diagnosis and improvement exercises, it is essential that the executives:
- Increase investment in the required digital twin technologies
- Improve the pace of its business digitization.
- Upgrade their digital technologies to integrate the use of the required digital twin technologies.
- Integrate usage of artificial intelligence, robotics and machine learning technologies as part of its critical business operational culture.
- Train and improve the skillfulness of the employees to creatively use the available digital twin technologies as integrated with AI to create and deliver the desired values.
- Scan and recruit the best unique talents from its ecosystem to fill the internal skills gap and create the desired values using AI and digital twin technologies.
Through usage of such strategies, a business may not only be able to ensure successful new product development, but also improved competitiveness.
Cite: Okanga, B. (2025). Digital Twin: The New AI and Machine Learning Era’s Leverager of New Product Development. London: Cloud Analytika.
Further Readings
Analytics Insight. (2024). Youtube Video: Applications of Digital Twin to Transform the Healthcare Industry. https://www.youtube.com/watch?v=6nK1Yrf3lFc
Canorea, E. (2024). Digital Twins for improved product development. London: PlainConcepts. https://www.plainconcepts.com/digital-twins-product-development/
Cole, C. (2024). Aircraft design – Part 2: Leveraging a multidisciplinary digital twin. Helsinki: Siemens. https://blogs.sw.siemens.com/aerospace-defense/2024/07/17/aircraft-design-part-2-leveraging-a-digital-twin/
Geospatial World. (2024). Youtube Video: What is Digital Twin? How does it work? https://www.youtube.com/watch?v=iVS-AuSjpOQ
Jagtap, N. (2024). Digital twins: The new opportunity in product development. New Delhi: TATA Consultancy Services Limited. https://www.tcs.com/what-we-do/industries/manufacturing/blog/manufacturing-technology-role-of-digital-twin#:~:text=Digital%20twins%20reduce%20the%20time,the%20product%20development
Microsol Resources. (2024). Youtube Video: What is Digital Twin? https://www.youtube.com/watch?v=60eCpw0Toy4&t=11s
Scott, J. (2024). What Are Digital Twins and How Can They Be Used in Healthcare? Digital twin technology can help physicians and researchers better understand population health and even treat heart disorders. Vernon Hills: HealthTech. https://healthtechmagazine.net/article/2024/01/what-are-digital-twins-and-how-can-they-be-used-healthcare
Siemens. (2024). From outdated to trendsetting: Turning Nestlé’s aged food plant in Juuka, Finland, into a digital factory of the future with the Digital Enterprise. Helsinki: Siemens. https://xcelerator.siemens.com/global/en/industries/food-beverage/references/nestle.html